Money
Prices swell as economy bounces back
Industrialists cite higher cost of raw materials and freight charges for the upsurge in market prices.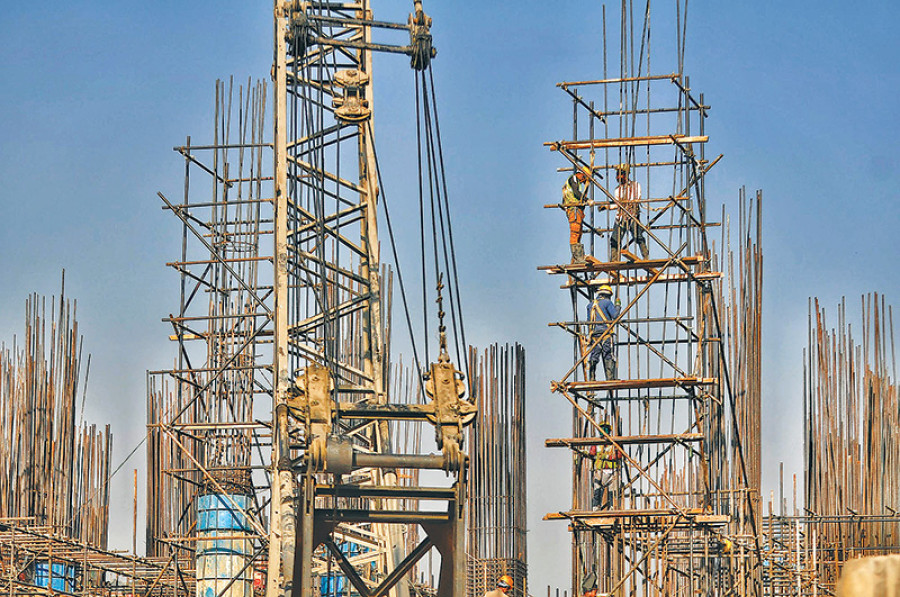
Madhav Dhungana
Until two years ago, you could buy a 50 kg bag of ordinary Portland cement for Rs650. Today, it costs Rs700. The price of Portland Pozzolana cement too has risen from Rs550 to Rs650 per bag. Other building materials like iron rods have also become dearer, up from Rs75 to Rs95 per kg.
Food products like edible oil and rice have become more expensive. Along with the price of manufactured goods, freight charges have gone up due to a shortage of truckers.
Cement and iron and steel factories say they have had to increase prices because of the higher costs of industrial raw materials. Transport entrepreneurs claim that the fare has gone up due to a sudden increase in production and market demand.
“Market prices of cement and iron and steel are not stable as they have surged within a week,” said Rajesh Kharel, seller of building materials and senior vice-president of the Siddhartha Construction Materials Entrepreneurs’ Association, Rupandehi.
“Normal price fluctuations due to specific reasons happen sometimes, but prices are shooting up unnaturally,” he said.
Domestic cement manufacturers say that the price of coal imported from South Africa and Australia, along with the cost of transporting it to Nepal from Indian seaports, has increased. Coal is used to make clinker, the raw material needed to make cement.
Uddhav Karki, general manager of Arghakhanchi Cement, claimed that the higher cost of imported coal and transportation to Nepal had pushed up production costs.
According to him, the price of imported coal has increased from $62 to $88 per tonne. The coal arrives at Haldia port in India from where it is carried by truck to Bhairahawa, which costs Rs3,400 per tonne, up from Rs2,500 previously.
Karki said that the transportation cost from Birgunj to Bhairahawa had increased from Rs950 to Rs1,000 per tonne previously to Rs1,200 currently. “This way the cost of production will go up automatically,” he said.
According to Arun Goenka, managing director of Everest Rolling Industries, iron and steel have become more expensive because the price of iron ore in India has jumped by 55 percent. Goenka claims that the price hike is due to increased global demand for industrial raw materials as stalled projects and construction work are now resuming.
“The price of iron ore in India has swelled from IRs1,600 per tonne to IRs2,700,” said Goenka who is also vice-president of the Siddhartha Chamber of Industry and Commerce. “The price is expected to go up further,” he added.
China which used to export iron has started importing it to control pollution, and the projects and construction work which had come to a stop due to Covid-19 have started resuming, leading to excessive demand for raw materials globally and a hike in prices, he said. Bhairahawa and adjacent areas in the Tarai account for a large share of the production of cement, iron and steel.
Of the 61 cement factories in the country, 11 are located in Rupandehi, four in Nawalparasi, nine in Kapilvastu, one each in Arghakhanchi and Rolpa, and two each in Dang and Banke.
Hongshi Cement has its production plant in Nawalpur of East Nawalparasi. Five large rotary technology cement factories are also being added.
Rupandehi has a daily cement production capacity of 9,800 tonnes, Nawalparasi 6,850 tonnes and Kapilvastu 6,000 tonnes.
There are 30 steel mills currently operating in the country. More than half of them are located in Lumbini province, with the highest number in Bhairahawa and surrounding areas.
Manufacturers of construction materials have been operating at 60 percent capacity due to the lockdown and subsequent labour problems.
Karki said that all industries had started increasing output after the stay-home order was eased and workers returned to work.
“Following the resurgence in construction work including home building that had ground to a halt during the virus lockdown, the construction industry is in an upbeat mood,” he said. If no new hurdles emerge in the days ahead, all industries will be operating at 100 percent capacity, he added.
According to the Bhairahawa Customs Office, Nepal had imported 255,000 tonnes of coal worth Rs3.10 billion between mid-July and December-end of the current fiscal year while imports in the whole of the last fiscal year totalled 780,000 tonnes valued at Rs10.69 billion.
Imports of MS billet reached 347,000 tonnes worth Rs8.22 billion during the review period compared to 537,000 tonnes worth Rs26.72 billion during the whole of the last fiscal year.
As per Purna Prasad Lamsal, information officer at the Bhairahawa Customs Office, the price of MS billet has gone up by $52 per tonne in the past one month. Coal for industry used to cost Rs3.50 to Rs6 per kg, but now the price has gone up to Rs8 to Rs9 per kg, he said.
Coarse and fine rice have become dearer by Rs6 per kg while soybean oil costs Rs60 per litre more.
Along with the price of goods, freight charges from Bhairahawa to other places have also increased.
Transporters say the cost of carrying goods from Bhairahawa to Kathmandu has gone up to Rs23,000 to Rs24,000 per 10 tonnes from Rs19,000 to Rs20,000 previously.
Freight charges from Bhairahawa to Pokhara have swelled to Rs21,000 from Rs17,000 to Rs20,000. The cost of transporting cargo has been increasing from mid-December as goods carriers are difficult to come by, insiders said.
Arjun Bhusal, vice-president of the Western Truck Entrepreneurs Association, said it used to take a day to reach the destination, but now it takes two days due to bad roads damaged during the rainy season.
Demand for goods has increased drastically after slowing down during the lockdown, and there aren’t enough goods carriers to go around. The government has not carried out any investigation to check whether freight charges have increased due to lack of trucks or an increase in demand as there has been no increase in the price of price.
Government bodies are reluctant to adjust prices by analysing the rise in prices of imported industrial raw materials, corresponding production costs and rising prices of manufactured goods. Neither the federal government nor local bodies have made the monitoring process effective.
Anil Sharma of Siddharthnagar-9 said prices could be increased in the past only with permission from the local administration after showing sufficient reason, but now entrepreneurs have been jacking up prices at will without any valid reason.
Kharel also said that the price hike in the market was due to the inaction of the monitoring regulatory body. According to him, no one has shown any interest in checking how high the price of raw materials has gone up, what the production cost is, how much profit entrepreneurs make and what is their sales volume.
Pitamber Ghimire, chief district officer, said that all entrepreneurs should keep a mandatory price list if the price goes up; and if they make a profit of more than 20 percent, action will be taken against them under black market laws.
He said that discussions had been held with the concerned businessmen and stakeholders after receiving complaints about the rise in the price of iron rods. “We will also monitor the market to prevent cartels under the pretext of rising raw material prices,” Ghimire said. “The reason behind the increase in transportation costs will also be investigated.”