Money
Hetauda Cement aims to generate Rs 200m in profit
State-owned Hetauda Cement Factory earned a profit of Rs40 million in the last fiscal year, despite encountering problems triggered by the trade embargo.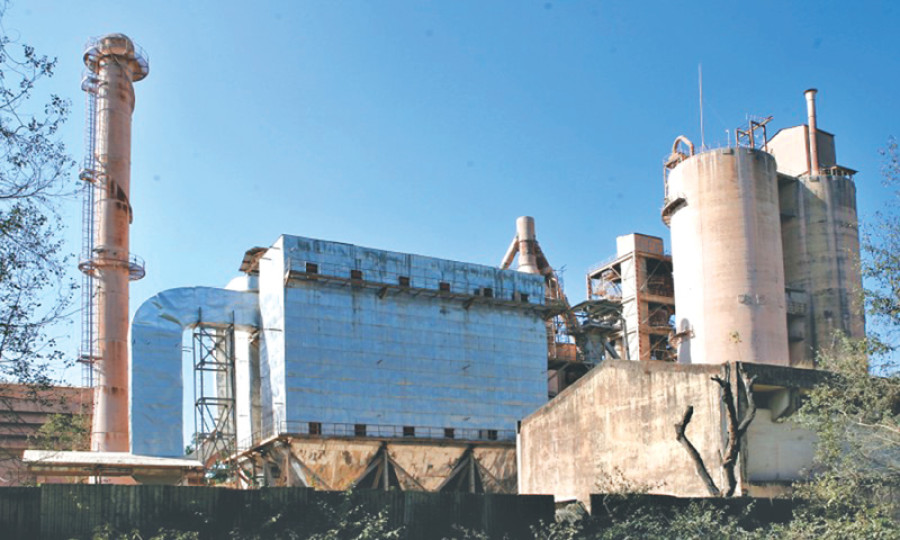
Pratap Bista
State-owned Hetauda Cement Factory earned a profit of Rs40 million in the last fiscal year, despite encountering problems triggered by the trade embargo.
The company has set a target of generating Rs200 million in profit in the current fiscal year by significantly reducing the production cost.
The cement factory was forced to shut down its operation for five months in the last fiscal year due to shortage of coal triggered by the trade embargo. But it is optimistic about enhancing its performance this year because of hike in cement price.
Although the cost of producing 50 kg of cement has gone up to Rs654 this year from Rs586 a year ago, retail price of cement has also gone up, according to Prem Shankar Singh, general manager of Hetauda Cement. “This hike in retail price will help us meet the target of generating profit of Rs200 million in this fiscal year,” said Singh.
To increase its profit, the factory plans to operate at 60-65 percent of its capacity in this fiscal year, as against 30 percent in the last fiscal year.
“If Nepal Electricity Authority provides power on a regular basis, we can achieve this target,” said Singh.
The factory has set a target of producing 150,000 tonnes of clinkers and 3.12 million 50-kg sacks of cement in this fiscal year, which will end in mid-July.
In the first eight months of the current fiscal year, the factory produced 92,000 tonnes of clinkers and 1.8 million sacks of cement.
In 2007-08, the factory had successfully operated at 53 percent of its capacity.
During that time, its net profit stood at Rs90 million. The profit increased to Rs110 million in 2009-10. However, it incurred losses for three consecutive years from 2012-13 to 2014-15.
Last fiscal year, the factory had produced 1.65 million of sacks of cement and 70,000 tonnes of clinkers.
“The amount of cement and clinkers produced in the last fiscal year has already been produced in the first eight months of this fiscal year,” said Raghu Raman Neupane, chairman of Hetauda Cement Factory.
The factory established three decades ago has been paying electricity bill of Rs30 million each month. The factory management and the board have been making efforts to reduce the cost of production.
According to the officials, the factory has been facing problems in cutting down production cost after the government announced 25 percent hike in employees’ salary this fiscal year. Also, use of old machines, which consume extra energy, is adding up to production cost.
More than 221 kilowatts of power is required to produce a tonne of cement at the factory. In contrast, private factories are using 95-100 kilowatts of electricity to produce the same amount of cement.
“We have to replace old machines to reduce power consumption,” said Singh. The factory currently employs around 395 people.