Entertainment
The history of Dachi Appa and Ma appa bricks
There is more to just the intricate wood and stone carving that adorn our temples, there is another crucial aspect that makes up the very fabric of these temples: The very special bricks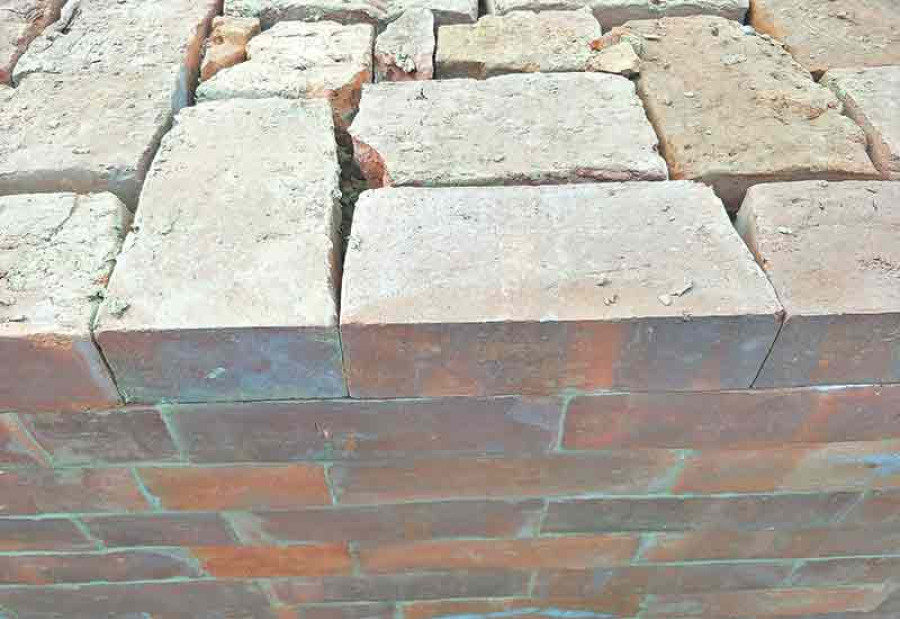
Sophia L Pandé
When it comes to our beloved temples, the majority of which are built in the traditional Newar style of architecture, we tend to think that these temples are emblematic of the intricate wood carving that adorns them, or the stone carvings, that are part of the make-up. What we do not know is that there are, in addition to these important elements, another crucial aspect that makes up the very fabric of these temples: the very special bricks.
Developed in the Malla Period ranging from 1200 onwards to 1768, when Prithvi Narayan Shah conquered the valley, these bricks that make up the temples can be divided into two main kinds, the dachi appa, or veneer bricks, known in Nepali as teliya ita, and the ma appa, or structural bricks.
The dachi appa bricks are especially fired at very high temperature, are darker red in colour, and have a glossy finish that makes them perfect as veneer bricks, those used for the seemingly “polished” side or façade of the tiered Newar temples and palaces. They also have a special shape; the front of the brick is a perfect rectangle while the sides taper with the width. This shape must have been perfected by trial and error over years by the Newars, mainly to create the smallest possible gap between the bricks for the façade so that the finish could be as homogenous and elegant as possible with no clumsy mortar peeking through the join of the bricks.
Traditionally, the Newars would use a special kind of mortar known as silay, which was made up of pine resin, mixed with vermillion to make it match with the tone of the bricks. Today a more easily available mud mortar made of yellow mud and water is used for the pointing of the bricks façade.
The ma appa bricks follow the dachi appa bricks in length, but vary in width and thickness, with the dimensions of the dachi appa brick being 8 inches by 4 inches by 2 inches in comparison to the ma appa which is 8 inches by 5 inches by 1 and ¾ inches. The common, local, red brick we use today for building our homes is 9 inches by 4 inches by 2 inches.
Bricks are made by collecting black clay, which is now extremely hard to find, most of it having been used up in the valley, and mixing that clay with water. Traditionally, the clay and water would be mixed by hands and feet, but now this is done mechanically with machines, so sometimes the homogeneity is compromised, with bits of stone and rubble making their way into the moulds. The mixed clay is then placed in the mould and left to sun-dry before firing. The sun drying process is crucial, the bricks must only be placed in the mild sunshine, therefore after Baisakh, the Nepali month, the bricks are no longer exposed to sunlight; it is too strong. After 2-3 weeks the bricks are ready for drying. Some special bricks, such as plinth bricks, which are used for the edges, such as in the brick tiled courtyards of the restored Babar Mahal Revisited, must be sun-dried for six months so that they are hard enough to withstand the wear and tear of edges. These bricks are large, their dimensions are 18 inches by 10 inches by 5 inches; in the Newar language, depending on where you are, Kathmandu, Patan or Bhaktpur, these bricks are called pha apa or loh apa.
People who work with the traditional dachi appa and ma appa bricks, such as Bijay Basukala and Raju Roka at the Kathmandu Valley Preservation Trust (KVPT), which is currently at work on eight projects in the Patan Durbar Square and the Kathmandu Durbar Square, lament the time when even local bricks were cut with a knife instead of using moulds, that cutting process made the brick flatter and the dimensions more precise. Today the ma appa and the dachi appa bricks can only be found in the factories of Hira Kaji Maharjan who makes the ma appa bricks in Thimi and the dachi appa bricks in Satungal, near Thankot.
For those working with these traditional bricks the KVPT has included an entire, detailed section on the ma appa and dachi appa bricks in their publication on the Sundari Chowk restoration (2006-2016) where they dealt with numerous issues such as figuring out the composition of bricks, mortar, the kinds of mud used in construction, the plaster, the punning, and the various washes. All are detailed in the publication, meant as a work in progress best practice manual for future restorers. The book also deals with the issues involved as bricks wear over the centuries in these precious historic buildings, encountering problems such as biological growth, bulging, crushing and breakage, erosion, efflorescence, incompatible mortar, incompatible patches of brick, loose bricks, narrow replacement bricks, pigeon droppings, recent paint, reconstruction, replacement bricks, and perhaps the worst of all: rising cyclical damp from our yearly monsoons.
For those of us who are interested in every aspect of rebuilding and restoration, but are stumped about where to start learning, this publication is a good way to begin. Who knew that bricks could play such an interesting part in Newar architecture, and could be so fascinating?