Science & Technology
‘Yatri Motorcycles was born with a vision of providing no-compromise e-mobility’
Ashim Pandey on what it takes to successfully design, engineer, and fabricate electric motorcycles in Nepal.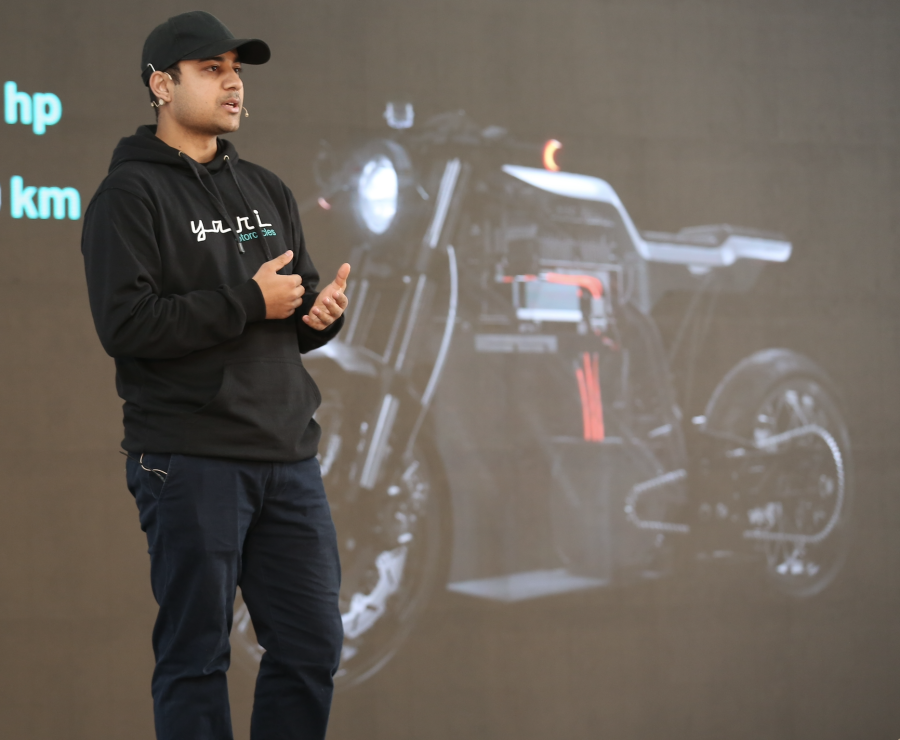
Prajesh SJB Rana
Yatri Motorcycles, an electric automotive tech company, recently released two products in the Nepali market: the P-0 and P-1 electric motorcycles. This release was met with polarising reviews, some applauding the engineering prowess of the company while others criticising the company for their expensive pricing.
We sit down with Ashim Pandey, Founder of Yatri Motorcycles, to further investigate these responses while also taking a critical look into what it takes to successfully design, engineer, and fabricate electric motorcycles in Nepal. Pandey has been at the centre of Yatri Motorcycles since its inception and has worn different hats from chief engineer, component designer, office administrator to human resource management over the years.
How did Yatri Motorcycles start and what has the journey been like?
In 2016, I found myself at a crossroad in my life. My dream had always been to design exotic cars at a European car company, a dream that I had successfully fulfilled. New adventures pointed to a different calling, I went on an amazing euro trip with my cousin, and now business partner, Batsal Pandey. He expressed interest in working together someday, which was the catalyst for my move back to Nepal and start my design studio at home.
In 2017, Yatri Motorcycles was born as an automotive tech company with a vision of providing no-compromise e-mobility. Influenced by the infamy of the Nepali hardware manufacturing industry, we started work on Project Zero (P-0) as a proof of concept—the best of our engineering prowess. P-0 was not an easy undertaking, we needed to build everything from scratch which required state-of-the-art research and a team of highly talented engineers ready to push boundaries in the field. The P-0 has never been a product to drive our business in terms of revenue, it’s our engineers making a statement.
Project One (P-1) is our first attempt at a commercial product. The knowledge, technology, and design engineered for the P-0 have been instrumental in the development of the P-1, although it’s far from an ideal mass-market product, we believe it to be a great start!
What have the research, development, and fabrication processes been like? What materials are the bikes made of?
The mechanical parts and brackets on both bikes are made out of automotive-grade Chromoly steel tubes, 6000 and 7000 series aluminum billets, and carbon fiber. We use CNC machines and other equipment to process these raw materials and machine them into final parts.
Even though raw materials are hard to come by locally, we’ve engineered many aspects of the bikes internally from the ground up. The trellis frame and carbon fiber fairings are all designed and developed in-house including the Vehicle Control Unit (VCU), electronics and electrical architecture. We also built our own batteries to drive our demanding engine along with the Battery Management System that controls it.
We stand by our engineering and the bikes come with an eight-year warranty on the P-0’s drive unit and a five-year warranty on the P-1’s. We also provide standard motorcycle warranty for three years on both bikes. Both bikes undergo rigorous testing to ensure lifespan and safety. We use industry-standard tests and certification guidelines to test fatigue characteristics, static and dynamic loads on full-scale vehicle testing and correlate those data with our Finite Element Analysis (FEA) results. This development cycle ensures that our vehicles are roadworthy not only in Nepal but all around the world.
During the initial launch, both Yatri motorcycles were criticised for pricing, what would you say justifies the price?
I would say the research and the engineering justifies the price. As I mentioned earlier, we have designed and developed numerous technologies from the ground up, pair that with all of the premium components used and it drives up the cost.
Research is never cheap, and for this project, we took on the arduous task of designing battery packs that perform on a league of their own. Designing high-output battery packs that can power engines that achieve high torque and speeds is not easy nor cheap. There are numerous such caveats in every sub-system that adds to the cost, unfortunately, most of the general public will be oblivious to this and will not be able to appreciate the engineering effort and cost that goes into a project like this.
The P-1 is our first attempt at scaling down for a market-friendly product and we have already started efforts for P-2, the first smart electric scooter of Nepal. We plan to design the P-2 to be a budget-friendly electric vehicle; however, the bigger challenge is to streamline development while finding better ways to work with government bodies, policymakers, supply-chain partners, and financial institutions.
What are the software implementations on the bikes and how do they synchronise with the accompanying smartphone app?
Our motorcycles are designed to seamlessly integrate into the user’s digital life. Vehicle vitals and smart data are displayed on the smart dashboard while also being mirrored to our Yatri Hub smartphone app. The integrated systems work closely with our VCU to reliably and accurately monitor all subsystems of the bike.
The Hub and the integrated system communicate over both Bluetooth and the Internet. The wide range of the internet makes it possible for users to monitor vehicle status, commute data, charge levels and even savings over fossil fuels while far away from their vehicle.
The app also plays a vital role in after-sales services, enabling riders to book pick-and-drop service and maintenance appointments. The app also integrates with our charging stations, smartly monitoring routes and suggesting routes with charge stations during low battery. We are committed to the Hub and plan to release all future services through it.
How secure are the VCU and Yatri Hub against cybercriminals?
With a product like a smart vehicle, we have to consider all kinds of scenarios, and the protection of our systems and our riders is very important. We have secured access points like CAN Bus, debug ports, mobile app security, and OTA update packages for future security updates. We have also secured our systems with two-factor authentication for certain features and have signed OTA packages. We understand that no system is 100 percent secure, which is why we’re narrowing vulnerabilities and patching them via regular updates.
Do the bikes have smart vehicle capabilities like traffic monitoring and crash detection? What kind of monitoring and sensory hardware have you used to facilitate this?
Yes, both of our bikes have smart vehicle capabilities. Our engineers have equipped the bikes with tons of sensors that allow both vehicle tracking and crash detection. Along with the many sensors and GPS, the bike can monitor lean angles and send out emergency messages to Yatri HQ and the rider’s emergency contact in the case of an accident. Yatri bikes also feature a unique keyless start mechanism that doesn’t require a physical key for users to start their bikes. Other general smart capabilities like auto start and off, odometre, and automatic turning off of the indicators are all part and parcel.
How effective are your batteries? Have you thought about environmental implications and sustainability of used batteries?
I would say that we’ve built a very effective Lithium-Ion battery that not only performs well but lasts for a long time. Since the batteries are built in-house, we source individual cells from suppliers in North America, China, and South Korea and put them together to build a battery that can easily last for over 12 years before a 20 percent range drop with 10,000 km/year commute which is about 120,000 km, with an expected 150,000 km with good riding practice.
However, not all lithium batteries are apples-to-apples. Some cheap electric motorcycles and scooters use Lithium-Ion batteries that are rated for lower charge and discharge capacity which provides low power while taking an excessively long time to charge. We’ve designed our batteries for high discharge and charge—rating cells that push more than 700A of current (almost 10X more than average market cells) for blistering power while also supporting quick charge over DC.
When our batteries eventually reach their end cycle, we repurpose them as electric storage solutions for our charging stations. These buffers are essential to relieve the load from the grid while also giving second life to used batteries. Moreover, Lithium-Ion batteries are recyclable, 80 percent of the cells we use can be recycled and we’re working with our cell suppliers to further facilitate cell recycling.
What are your plans for the future?
We aim to keep investing in R&D, evolving, and improving. To expedite the production of our mass market products, we have begun construction of Nepal’s very first state-of-the-art research and development centre, which will house both the New Product Development (NPD) facility and product assembly lines. This will minimise cycle time between development and manufacturing while cutting down our time-to-market significantly. We project that we will be able to roll out 3,000-4,000 units by the end of next year. Developing a mass-market electric vehicle is only one side of the coin. Our priority in 2021 is also to create a strong network of Yari charging stations across the country.
We have already developed our charging stations and have tested them with the P-1, which means that scaling them up for larger networks of charging stations is the most important development for us before the rollout of P-2 in 2022.